Pengeluar penggelek salutan
Richconn khusus dalam pembuatan penggelek salutan. Penggelek salutan kami digunakan untuk membantu pelbagai substrat seperti kertas, kain, Filem, foil dll. bersalut seragam. Setelah bertahun-tahun penyelidikan dan pembangunan yang mendalam, Teknologi pemprosesan kami telah matang. Sistem kawalan kualiti syarikat kami telah diperbaiki secara komprehensif, menjamin kestabilan dan konsistensi penggelek salutan kami.
Kami berjanji kepada anda produksi yang cekap dengan penggelek salutan unggul kami. Aplikasi penggelek salutan kami boleh terdiri daripada kesan salutan seragam ke keperluan salutan khas. Tidak kira dengan cara anda menggunakan penggelek salutan kami, Anda boleh merasa yakin bahawa penggelek salutan Richconn sentiasa membawa kualiti premium ke proses pengeluaran anda. Pilih RichConn untuk memberikan aplikasi salutan anda sebagai rangsangan kuasa!
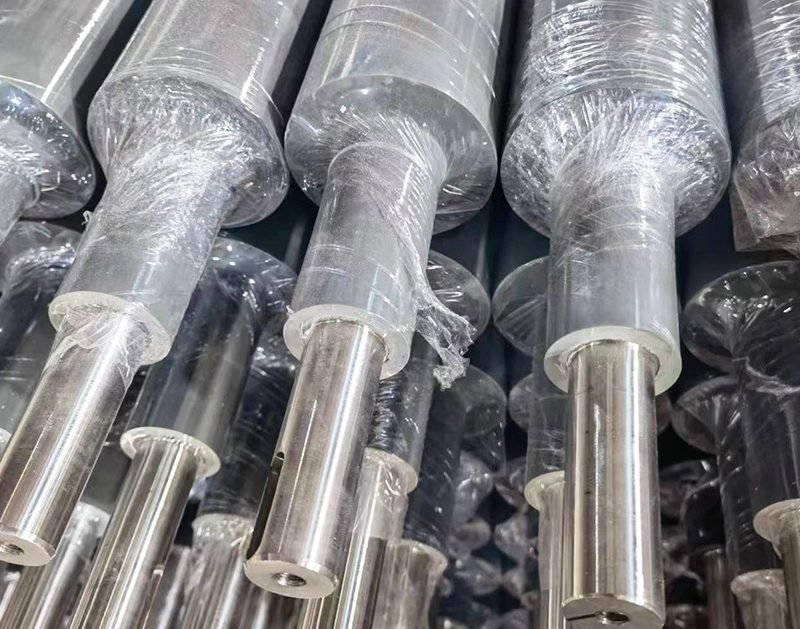
Paparan produk
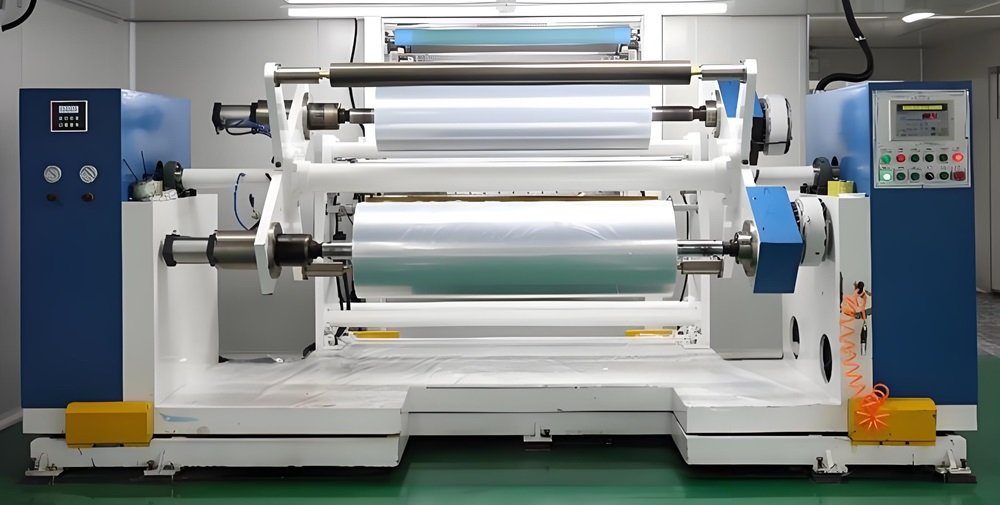
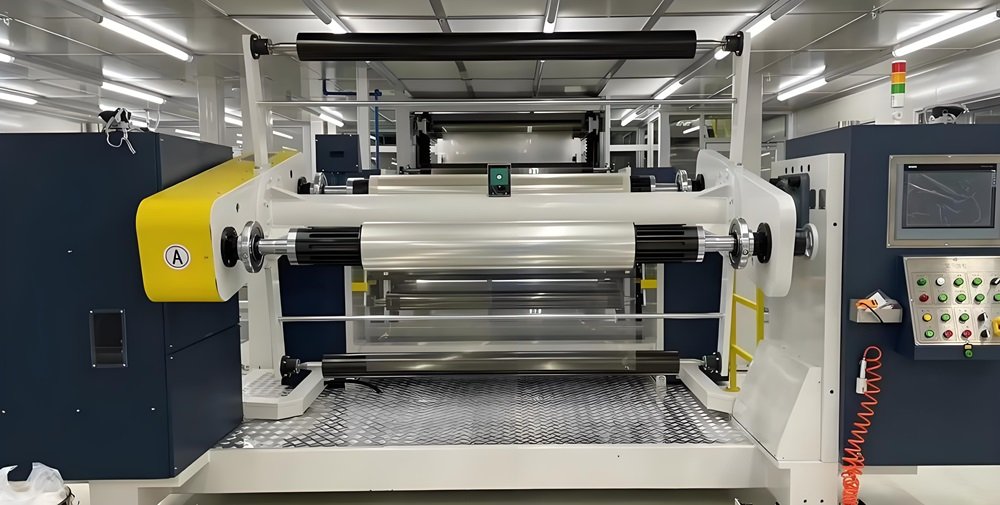
Apa yang perlu dipertimbangkan semasa memilih roller salutan?
Elemen utama | Penerangan | Pelarasan dan penjelasan untuk keperluan yang berbeza |
---|---|---|
Bahan | Bahan roller salutan mempengaruhi ketahanan, Pakai rintangan, dan kualiti salutan | Bahan biasa: Keluli tahan karat, getah, seramik, poliuretana, dll. Bahan yang sesuai dipilih berdasarkan sifat kimia salutan untuk mencegah kakisan atau kerosakan semasa proses. |
Ketepatan permukaan | Kelancaran permukaan dan ketepatan berkaitan secara langsung dengan keseragaman salutan dan kawalan ketebalan | Kekasaran permukaan biasanya dikawal pada tahap mikron. Proses pengisaran dan penggilap meningkatkan ketepatan, Terutama penting untuk aplikasi yang memerlukan ketepatan salutan yang tinggi. |
Pakai rintangan | Roller salutan mesti sangat tahan lama untuk menahan jangka panjang, Penggunaan frekuensi tinggi | Bahan-bahan yang tinggi (seperti salutan seramik atau keluli tahan karat yang keras) atau salutan tahan haus memanjangkan hayat perkhidmatan, mengurangkan kekerapan dan kos penyelenggaraan. |
Ketepatan salutan | Kawalan ketebalan salutan yang tepat memastikan kualiti salutan yang konsisten | Pelarasan dalam diameter roller, tekanan, dan kelajuan, Digabungkan dengan sistem kawalan mekanikal ketepatan (Mis., kawalan gelung tertutup) Benarkan pelarasan yang baik, Terutama berguna untuk salutan filem yang tepat. |
Tekstur permukaan | Tekstur permukaan secara langsung mempengaruhi lekatan dan keseragaman bahan salutan | Tekstur tersuai (seperti mesh atau kemasan licin) Berdasarkan kelikatan salutan dan ketidakstabilan meningkatkan keseragaman salutan; contohnya, Kemasan yang lancar sering digunakan untuk salutan UV untuk memastikan gloss. |
Rintangan kimia | Permukaan roller mesti menahan kakisan dari lapisan kimia yang berbeza | Penggelek salutan khas memerlukan rawatan anti-karat, atau bahan tahan kimia (seperti salutan Teflon) untuk menahan lapisan yang sangat menghakis, meningkatkan kestabilan dan keselamatan. |
Keseimbangan dinamik | Roller harus mengekalkan kestabilan pada kelajuan tinggi untuk mengurangkan getaran dan penyimpangan | Penentukuran mengimbangi dinamik memastikan kestabilan pada kelajuan yang berbeza -beza, mencegah salutan yang tidak rata semasa operasi berkelajuan tinggi, penting untuk aplikasi dalam percetakan dan elektronik. |
Toleransi suhu | Roller harus menahan suhu tertentu tanpa ubah bentuk atau salutan yang tidak sekata | Beberapa proses salutan memerlukan pemanasan atau penyejukan, memerlukan tinggi- atau bahan tahan suhu rendah (seperti salutan tinggi atau sistem penyejukan) Untuk mengekalkan kestabilan salutan. |
Aplikasi Industri Roller Coating
- Industri Kertas
- Industri percetakan
- Industri tekstil
- Industri Elektronik
- Industri automotif
- Industri pemprosesan logam
- Industri Filem Plastik