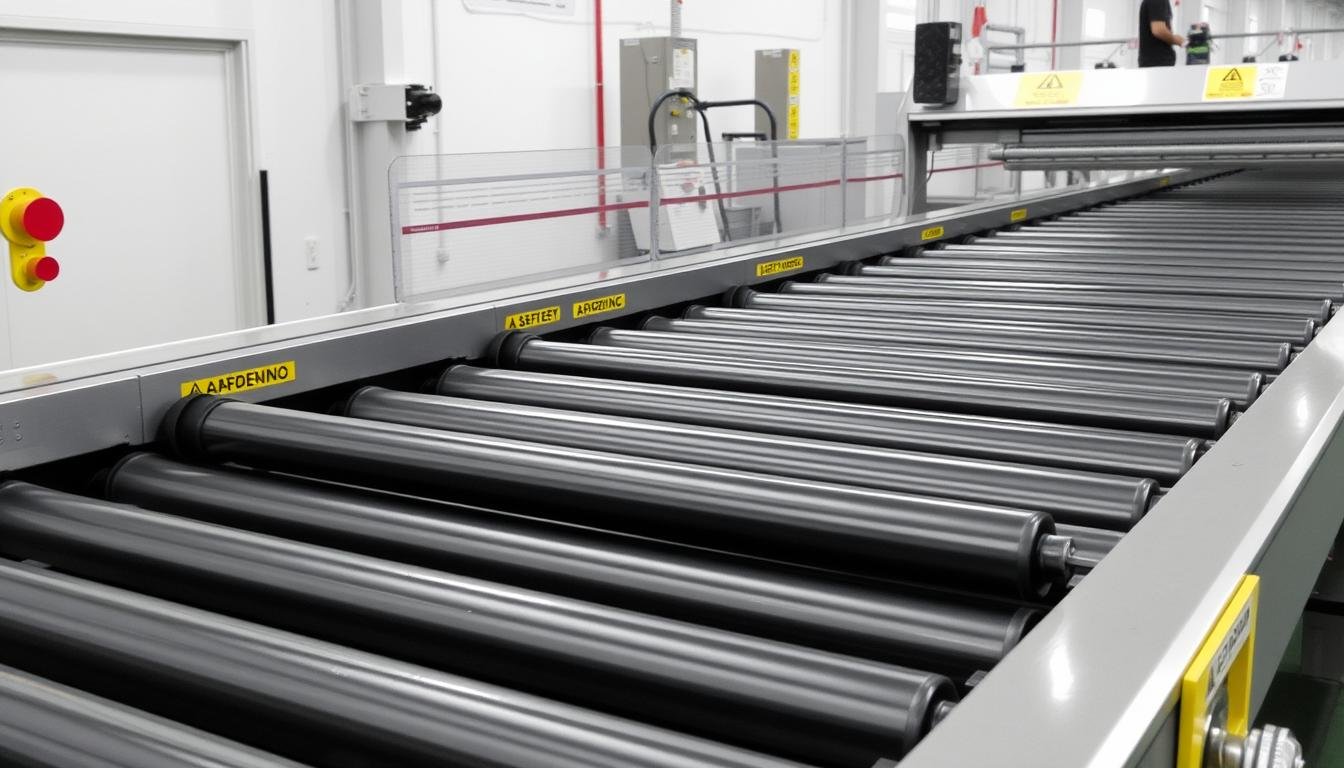
Penggelek perindustrian adalah kunci dalam banyak langkah pembuatan. Mereka membantu membuat proses lebih cekap dan produktif. Dari masa ke masa, Teknologi roller telah bertambah baik. Sekarang, Kami mempunyai penggelek maju untuk keperluan yang berbeza dalam industri.
Sistem roller industri membantu menjadikan sesuatu lebih baik dan lebih murah. Mereka juga menjadikan produk yang berkualiti tinggi. Knowing how industrial rollers work can help businesses improve. This way, they can stay ahead in the market.
More and more companies are using industrial rollers in their work. They want to make their operations better and cheaper. As we need better solutions, the role of industrial rollers will grow. This will lead to more innovation and growth in many fields.
Understanding Industrial Rollers: Basic Principles and Functions
Industrial rollers are key in many fields like manufacturing and material handling. Knowing about their design, mechanics, and parts is important. The design affects how well they work, how long they last, and their performance.
The main parts of industrial rollers are the roller body, galas, and drive systems. These parts help rollers work smoothly. This is why they’re so important in many industrial processes. Learning about rollers helps industries work better, be more productive, and save money.
- Roller materials: The choice of material for the roller body affects its durability and resistance to wear and tear.
- Bearing types: The type of bearing used in industrial rollers impacts their efficiency, noise level, and maintenance requirements.
- Drive systems: The drive system used to power industrial rollers can significantly influence their performance, kelajuan, and control.
By thinking about these points, industries can make smart choices when picking and using industrial rollers. This knowledge helps them improve their operations.
Types of Industrial Rollers in Modern Manufacturing
Penggelek perindustrian are key in many manufacturing steps. They come in different types for various industries. This includes food, tekstil, and metals.
These rollers have many uses. Conveyor rollers move materials, while processing rollers shape them. Finishing rollers polish the final product.
Rollers are vital for making products efficiently. They help in many production stages. This has made products better and more consistent.
- Conveyor rollers for material handling
- Processing rollers for shaping and forming
- Finishing rollers for polishing and refining
The variety of industrial rollers has changed the manufacturing world. It helps companies make quality products quickly. As technology grows, so will the need for new rollers and processes.
What Does an Industrial Roller Do in Various Production Processes
Industrial rollers are key in many production steps. They help in material handling, processing, dan penamat. Their uses span from making goods to getting them to customers. They make production smoother and more efficient.
Industrial rollers are very important in making things. They help move, process, and finish materials. Material handling is where they shine, helping to move heavy items safely.
Material Handling Applications
In material handling, rollers help move and sort items. They fit into conveyor systems for automated handling. This is vital in fast-paced industries like manufacturing and logistics.
Processing and Finishing Operations
Rollers also aid in processing and finishing, like printing and cutting. They apply pressure or heat to materials. This makes them a flexible tool in many production steps.
Conveyor System Integration
In conveyor systems, rollers move materials between production stages. They link machines and processes, automating lines. This boosts efficiency and cuts down on mistakes and accidents.
Industri | Application | Benefits |
---|---|---|
Manufacturing | Material handling and processing | Increased efficiency, reduced costs |
Logistics | Conveyor system integration | Improved accuracy, reduced errors |
Distribution | Material handling and sorting | Increased speed, reduced damage to goods |
Essential Components and Design Features
Industrial roller design includes key parts that make it work well. These parts are the roller’s material, galas, and drive systems. The size and shape of the roller matter a lot for its use.
The bahan used can change based on the job. For heavy tasks, steel or stainless steel is often chosen. For lighter jobs, aluminum or plastic might be better. The galas are also important. They help the roller move smoothly and reduce friction.
Some important design features of industrial rollers are:
- Roller diameter: helps handle heavy loads and fit in tight spots
- Roller width: makes the roller stable and handle wide loads
- Roller length: lets the roller manage long loads and curved paths
Knowing about the parts and design of industrial rollers is key. It helps pick the right one for the job. This way, industries can work better and more efficiently.
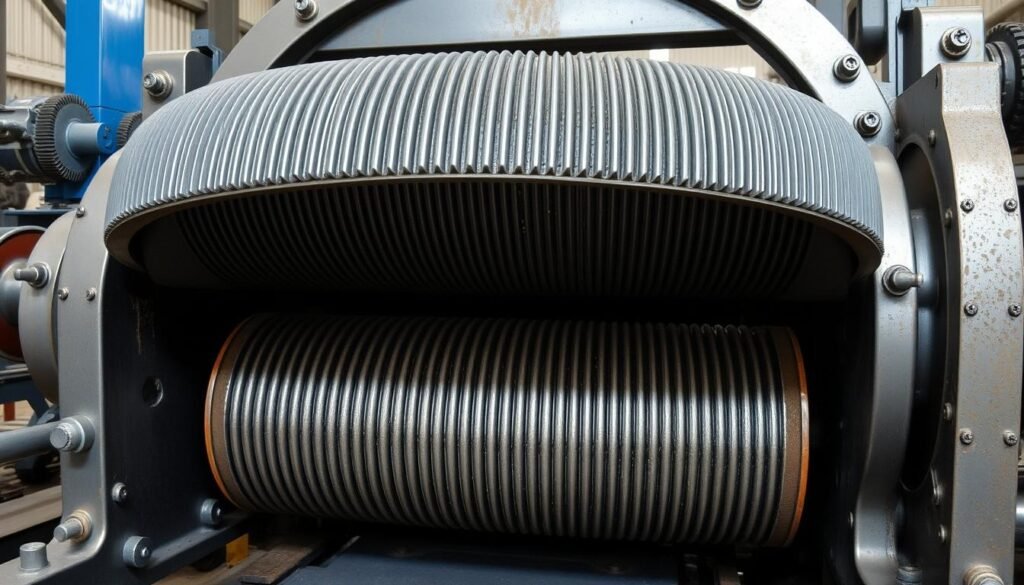
Industrial rollers play a critical role in various industries, and their design features can significantly impact productivity and efficiency.
Komponen | Penerangan |
---|---|
Roller Material | Affects durability and resistance to wear and tear |
Galas | Enable smooth rotation and reduce friction |
Drive Systems | Power the roller’s rotation and movement |
Industry-Specific Applications and Uses
Industrial rollers are used in many manufacturing industries. They meet different needs, from printing and paper to metal and food production. Knowing how they are used in each industry helps us use them better.
Each industry has its own needs for industrial rollers. For example, in printing and paper, rollers are made to handle paper and ink well. In metal processing, they must handle high temperatures and heavy loads.
Printing and Paper Industries
In printing and paper, rollers are key. They help cut, fold, and print paper products. These rollers are made to work well with paper and ink.
Metal Processing Applications
In metal processing, rollers shape, cut, and form metal. They are made to handle high temperatures and heavy loads. This makes them perfect for metal work.
Textile and food processing also use industrial rollers. In textiles, they cut and fold fabric. In food, they package and label products.
Industri | Application | Roller Type |
---|---|---|
Printing and Paper | Cutting, Folding, Printing | Coated Rollers |
Metal Processing | Shaping, Cutting, Forming | Heavy-Duty Rollers |
Textile Manufacturing | Cutting, Folding | Specialty Rollers |
Pemprosesan makanan | Packaging, Labeling | Sanitary Rollers |
Maintenance and Performance Optimization
Keeping industrial rollers in good shape is key to their performance and longevity. This includes regular lubrication, alignment, and balancing. These steps help avoid wear and tear. A set maintenance schedule helps avoid costly repairs and keeps operations running smoothly.
It’s also important to optimize roller performance. This means keeping an eye on how they’re doing and making adjustments as needed. Roller upkeep is a continuous effort that demands focus and a high standard of care.
- Regular lubrication to reduce friction and wear
- Proper alignment to prevent uneven wear and tear
- Balancing to ensure smooth operation and minimize vibration
By focusing on roller maintenance and performance, industries can boost efficiency and cut costs.
Industries should also adopt a proactive approach to roller care. This includes regular checks, maintenance, and repairs. Catching issues early can prevent major problems and keep production running. Investing in roller upkeep ensures they work at their best, leading to better efficiency and productivity.
Maintenance Task | Frequency | Importance |
---|---|---|
Lubrication | Weekly | High |
Alignment | Monthly | Medium |
Balancing | Quarterly | Low |
Benefits and Advantages of Industrial Roller Systems
Industrial roller systems bring many benefits and advantages to a company. They help improve productivity and save money. These systems make work more efficient and cut down on labor costs. They also help reduce waste and make production better.
The advantages of these systems are seen in many areas of production. This includes handling, processing, dan penamat. Some key benefits are:
- Increased throughput and reduced production time
- Improved product quality and consistency
- Reduced labor costs and minimized waste
- Enhanced safety features and reduced risk of accidents
Companies can get ahead in their markets by using these systems. They lead to more profit and growth. So, investing in industrial roller systems is a smart move for any business.
As companies look to improve their production, the need for these systems will grow. They offer many benefits and are key to the future of manufacturing.
Benefit | Penerangan |
---|---|
Productivity Improvements | Increased efficiency and reduced labor costs |
Cost-Efficiency Factors | Minimized waste and optimized production processes |
Quality Control Benefits | Improved product quality and consistency |
Safety Considerations and Best Practices
Keeping a workplace safe is key, and that includes making sure industrial rollers are safe. Following safety rules helps avoid accidents and keeps workers healthy. By managing risks well, companies can make their workplaces safer.
Important steps for keeping industrial rollers safe include regular checks, training workers, and following safety rules. Regular inspections can spot dangers before they cause trouble. Juga, training workers helps them know how to use rollers safely.
Here are some ways to keep operations safe:
- Do regular risk checks to find dangers
- Use controls to lessen risks
- Teach workers how to use rollers safely
- Keep rollers in good shape to avoid breakdowns
By focusing on safety and following these steps, companies can lower accident risks. This makes the workplace safer for everyone.
Risk Management Protocol | Penerangan |
---|---|
Hazard Identification | Find dangers linked to industrial rollers |
Risk Assessment | Figure out how big a risk each danger is |
Control Measures | Put in place steps to reduce or remove risks |
Conclusion: The Future of Industrial Roller Technology
The future of industrial roller technology looks bright. It’s set to see big changes and new ideas. The industrial roller technology world is changing fast. This is because of the need for better efficiency, sustainability, and automation in modern manufacturing.
New trends are coming, like smart sensors and predictive maintenance. These will make rollers work better and less often stop. Juga, new materials and designs will make rollers last longer and use less energy. This will make them key to future production.
The growth of Industry 4.0 and the Internet of Things (IoT) will change how we use rollers. We’ll get real-time data and smarter decisions. This tech will make rollers smarter, more flexible, and able to fix problems on their own. It will make making things more efficient and reliable.
The role of industrial roller technology in modern manufacturing’s future is huge. With ongoing research and a focus on new ideas, the possibilities for rollers are endless. They can help make production better, more quality, and more sustainable.
Soalan Lazim
What is the purpose of an industrial roller?
Industrial rollers are key in many manufacturing processes. They help move, process, and finish materials. This makes industries like printing and food processing more efficient and quality-focused.
What are the different types of industrial rollers?
There are many types of industrial rollers. You have conveyor rollers, processing rollers, and finishing rollers. Each type does a specific job in making things, like handling materials or shaping them.
How do industrial rollers work in production processes?
Rollers are used in many ways in making things. They move materials, apply pressure, and help with finishing touches. They’re key in systems that keep production smooth and consistent.
What are the essential components and design features of industrial rollers?
Rollers have core parts like the body, galas, and drive systems. Their design, like size and material, is made to fit the job. This ensures they work well and last long.
How can industrial rollers be maintained and their performance optimized?
Keeping rollers in good shape is important. Regular checks, like lubrication and alignment, help them work better. Juga, fixing or replacing worn parts is key to their long life.
What are the benefits and advantages of industrial roller systems?
Roller systems make production faster and cheaper. They help make products better and more consistent. This is why they’re so important in today’s factories.
What safety considerations are important for industrial roller operation?
Safety is very important when using industrial rollers. Following safety rules, managing risks, and training workers are all critical. They help keep everyone safe on the job.
What are the future trends and innovations in industrial roller technology?
The future of roller technology looks exciting. New tech like Industry 4.0 and green initiatives will play a big role. Expect better materials, smarter systems, and more efficient rollers that are also good for the planet.